Compared to non cathodic protection:
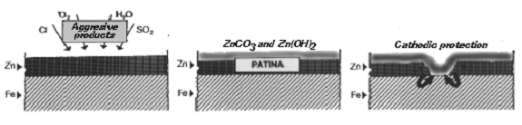
If the Unigalv layer is sufficiently damaged to expose the base metal below, the steel would form a layer of surface rust but no corrosion would take place beneath it. In other words if the surface discolouration was removed the steel below would not be pitted or eroded. This is called "throw" and enables Unigalv to protect bare metal up to 5mm away from where the coating ends, the same as HDG. Zinc sacrificial anodes used on the steel hulls of boats work on the same principle to protect metal in the surrounding area. Unigalv is simply a different form of these anodes and is therefore sometimes referred to as a "sheet-anode".
There are plenty of so-called zinc rich paints on the market which claim to provide active protection but to do this they must contain more than 92% zinc - many simply do not. Dry Unigalv contains a minimum of 95% pure zinc, the particles of which are significantly smaller than those found in most coatings. The Unigalv particles small size and elliptical profile ensures maximum contact between both the individual particles and the substrate. This greater density of zinc per given area combined with the near perfect conductivity of the binder ensures that charge flows through every millimetre that has been coated and therefore provides vastly enhanced cathodic protection.
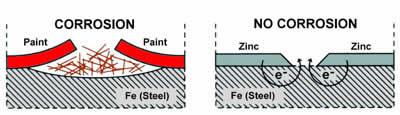
Passive Protection
Passive protection, such as paints and cladding, creates a "barrier" between the steel substrate and the elements. Once this barrier is compromised then the moisture and atmospheric salts will be able to start corroding the steel beneath the damaged area. This corrosion will then begin to creep extensively beneath the coating.
With Unigalv, the organic binder and the zinc oxide layer that forms on the surface create an impervious barrier by blocking the zinc's natural porosity with oxide particles. Unlike other passive coatings, once breached the zinc oxide layer simply renews itself by re-oxidising. This layer of oxides is the reason behind the matt appearance of Unigalv as opposed to the shiny hot-dipped finish and is the key to Unigalv's extra long life.
Predicted Service Life
The corrosion rates of zinc in various environments have been well researched over the years. As a result it is possible to chart the predicted service life for a zinc layer at a given DFT in a particular situation. The chart below is based on Hot-Dip Galvanised steel but, as it has already been explained in the Active Protection section, Unigalv performs at least as well as HDG in normal atmospheric conditions and even better in marine environments.
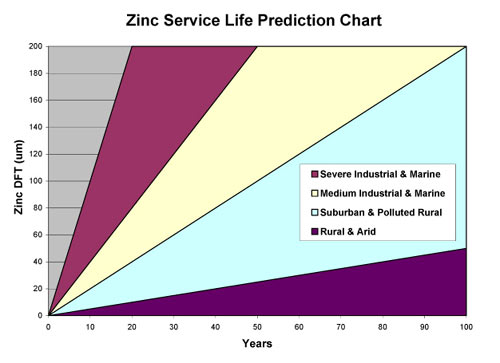
Duplex Systems
If Unigalv is used as part of a duplex system, i.e. is over-coated with another compatible product, the top-coat provides the initial barrier but the zinc oxide will form a secondary barrier if the first layer is compromised for any reason. As the topcoat becomes naturally porous over time, the Unigalv fills the pores from below with zinc oxides enabling the topcoat to last longer. It is because of this that Unigalv state that the lifetime of a duplex system can be 2.5 times the life of the Unigalv and the topcoat combined.
Re-Liquidising of Unigalv
Another of Unigalv's unique characteristics is its ability to re-liquidise when a new coat of Unigalv is applied to form a single homogenous layer. This ensures a massive cost saving in on-going maintenance because the old Unigalv layer does not have to be removed before re-coating with Unigalv. This also means that once the initial abrasive blasting has been completed the surface will never have to be blasted again.